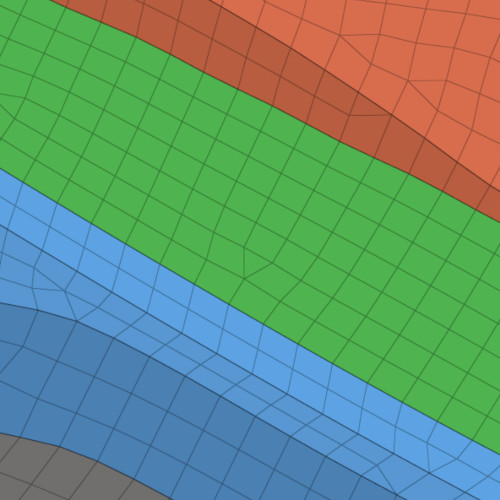
Facts about the project
Project manager: Dr. Karsten Reiter +++ Duration: 1.1.2023 until 31.12.2025 +++ Project funding: Federal Ministry for Economic Affairs and Climate Action (BMUV) Projektträger Karlsruhe (PTKA)
Status Quo & Outlook
The project began in spring 2023 with intensive collaboration between the working groups. After defining the geometry and the material properties to be used for a generic model to test the reduced basis method, initial tests were successfully carried out by the project partners. As classic tests of uncertainty analysis are impossible with complex models due to excessive computing times, a method was developed to estimate the uncertainty of model results on the basis of the distribution function of material properties using just a few model runs. A model geometry was created on the basis of site selection models in Switzerland, which is to be used for the complex reference model for the final test of the methods developed in the project in the last third of the project period. In addition, a 2-D model geometry was derived from it in order to compare different methods of discretising a computational mesh. Furthermore, this model will be used to investigate the influence of variable material properties, the mesh resolution, element type and element order.